双螺杆挤出机自1948年创制以来,直到20世纪60年代因其优异性能在大型制件挤出和配料共混中得到广泛应用,才开始迅速发展。其核心结构由两根啮合螺杆和“∞”字形料筒组成,工作原理与单螺杆挤出机不同,主要依靠正向输送作用强制物料前进。双螺杆挤出机在聚合物共混操作中具有独特优势:混炼效果显著,物料停留时间分布窄,挤出量大且能量消耗少。异向旋转双螺杆挤出机尤其高效,能将85%的机械能转化为热能,显著降低操作成本。
双螺杆挤出机创制于1948年。开始人们对这种设备的特性及用途缺乏了解而未被推广,直到20世纪60年代初期,双螺杆挤出机在挤出大型制件以及作为配料、共混装置方面显示了优异的性能,从此才得以迅速发展。
双螺挤出机的混炼挤出装置系由两根互相啮合的螺杆和一个"∞"字形料筒组成,其工作原理与单螺杆挤出机完全不同。物料在单螺杆挤出机中的输送,主要是依靠摩擦力;而双螺杆挤出机则主要是由两根相互啮合的螺杆在料筒内旋转时产生的"正向输送"作用,强制地将物料推向料筒末端。
双螺杆挤出机在进行聚合物共混操作时具有独特优点。
(1)混炼效果好 单螺杆挤出机混炼的效果不够理想,其原因是单螺杆挤出机的分散、混合作用仅依靠螺杆的压缩比及螺杆旋转时所产生的背压,以及由背压产生的反向流动所引起的。而双螺杆挤出机的两根互相啮合的螺杆在啮合处产生了强烈的剪切作用,对物料的分散与混合极有利。两螺杆的转向不同(异向旋转双螺杆和同向旋转双螺杆示意图分别见图 4-7 和图4-8),其效果也不同。对于异向旋转的双螺杆,物料在上下啮合处受到分流和剪切作用;对于同向旋转的双螺杆,一根螺杆的螺齿像楔子一样地伸入到另一螺杆的螺槽中,基本上阻止了物料由该螺槽进入到同一螺杆的相邻螺槽中去,大部分物料被强制地由一根螺杆的螺槽转移到另一根螺杆的螺槽中去。随螺杆的转动,物料在两螺杆之间反复转向,因而物料受到相当良好的混炼。据分析,在同向旋转双螺杆挤出机中,物料经过10个螺距后,混合次数可达22°之多。因此,即使参与共混的两聚合物的熔融黏度相差比较大,也能强制地混炼成为均匀的聚合物共混物。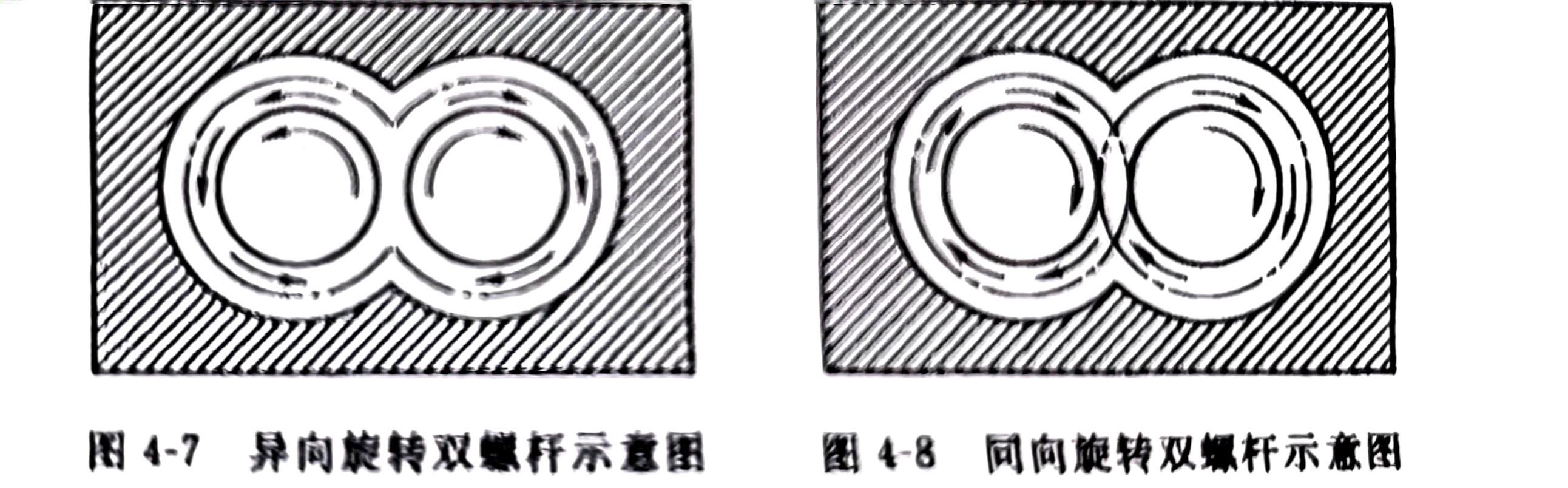
(2)物料在料筒内停留时间分布窄 物料在单螺杆挤出机中的流动有正流、逆流、漏流和横流等四种情况。逆流和漏流是由于机头、过滤板等存在的反压而引起的,它们将使得物料在挤出机料筒中停留时间分布变得较宽。而双螺杆挤出机的工作原理是"正向输送",所以物料在其中的平均停留时间比单螺杆挤出机少二分之一以上。同时,停留时间的分布范围也仅为单螺杆挤出机的五分之一左右,停留时间分布示意图如图 4-9 所示。因此,物料各部分在挤出机料筒内所经历的物理、化学变化过程大体相同,因而所得到的聚合物共混物的性能更均匀。双螺杆挤出机的两根螺杆互相啮合,旋转时彼此刮拭,从而可以避免物料对螺杆的黏附、缠包,这种效果称为螺杆的自清理作用;这种作用是使得物料在双螺杆挤出机中停留时间分布窄的另一原因。对于热敏性聚合物,停留时间的长短及停留时间分布的宽窄对共混操作十分重要。
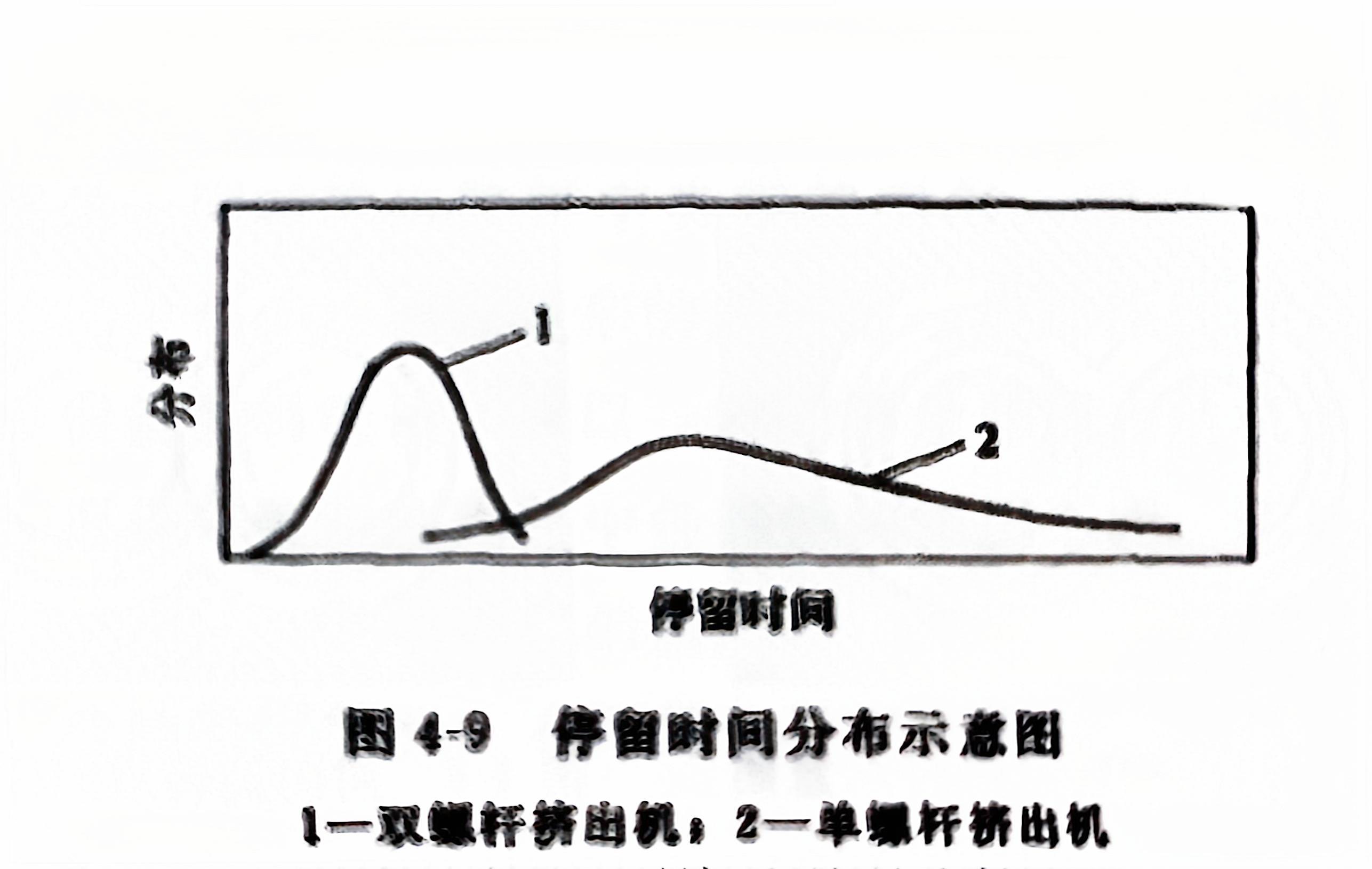
(3)挤出量大,能量消耗少 双螺杆挤出机的螺距小,螺槽深,有效螺槽容积比单螺杆挤出机大,加上有两根螺杆,故当螺杆直径和转速相同时,双螺杆挤出机的实际挤出量可达到单螺杆挤出机的3倍。双螺杆挤出机运转时,机械能可通过螺杆啮合处直接施加到其间的薄层物料上,使物料受到强烈的剪切作用,因而机械能可有效地转换为热能,从而提高了能量转化率。据报道,异向旋转双螺杆挤出机可将85%的机械能转化为热能,这对于降低聚合物共混操作的成本极为有利。目前,异向旋转双螺杆挤出机在生产上的应用已超过同向旋转双螺杆挤出机,图 4-10 所示为异向旋转双螺杆挤出机的螺杆形状示意图。该螺杆沿轴向分为6个部分,各部分直径相同,但螺距和螺纹数有所变化。其中第1部分为加料段,在此段加入物料,并将物料向前输送;第2~4部分为压缩段,起着压实和塑化物料的作用;第5部分为排气段,排出物料中所含气体以及物料可能分解而产生的气体;第6部分为计量段。物料在异向旋转双螺杆挤出机中几乎不出现圆周方向的流动而一直被推向前进,所以比同向旋转双螺杆挤出机的挤出量高约2倍,且物料滞流时间短。不过异向旋转螺杆的转矩大,设备要求更严格,价格也较高。
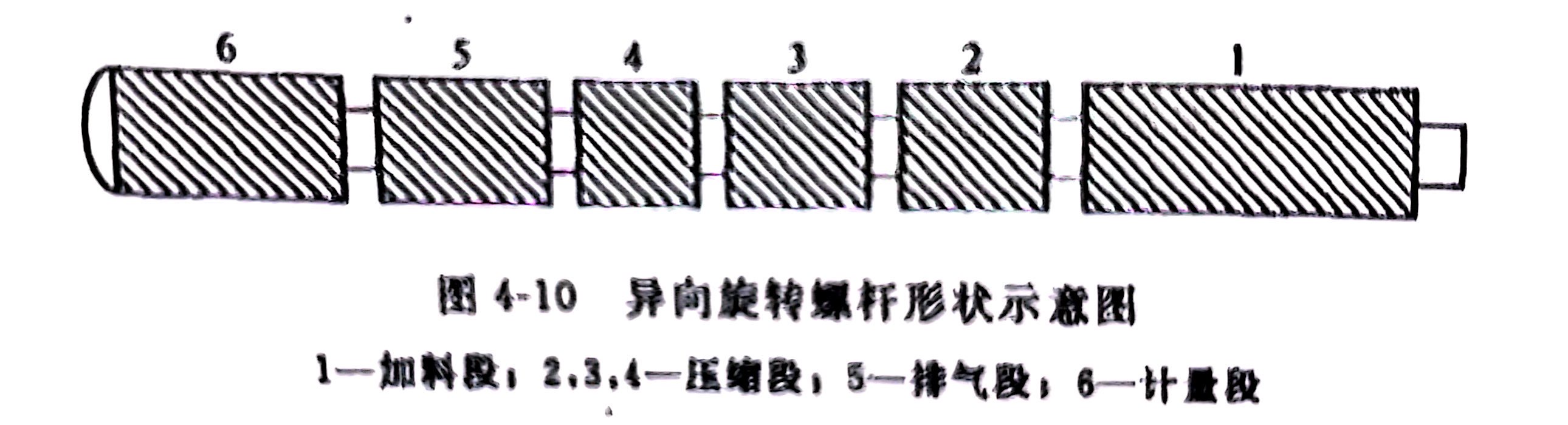