氧化锌在橡胶中广泛应用,但因其化学特性导致分散困难,可能引发胶料凝胶或焦烧。改善分散的方法包括表面处理、造粒、母炼胶法和优化加料顺序。表面处理和造粒能显著提升氧化锌的混炼性能,而母炼胶法通过分次添加氧化锌和水来提高分散度。加料顺序方面,应避免氧化锌与酸性配合剂同时加入,以防止结块。
氧化锌是胶料中应用最广的配合剂之一,一般用作活性剂,有时用作填充剂。由于其本身化学特性,氧化锌在橡胶中极易混人,但分散极难,有时会导致胶料凝胶或焦烧。据报道,检查胶料中分散不良的白色粒子,其中往往含有氧化锌。
氧化锌不易分散的原因是混炼时与生胶一样带负电荷,二者相斥。改善氧化锌混炼分散的方法有四种:表面处理、造粒、母炼、选择适当加料方式。
(1) 表面处理 一般采用表面活性物质,如低级脂肪酸一丙酸处理效果较好。美国的ZnO AT 和法国的 ZnO FT 均属此类产品。经表面处理的氧化锌在混炼时排胶温度较低,所需输人功率也较少(与未处理氧化锌相比),经表面处理的各种氧化锌混炼特性见表3-10。
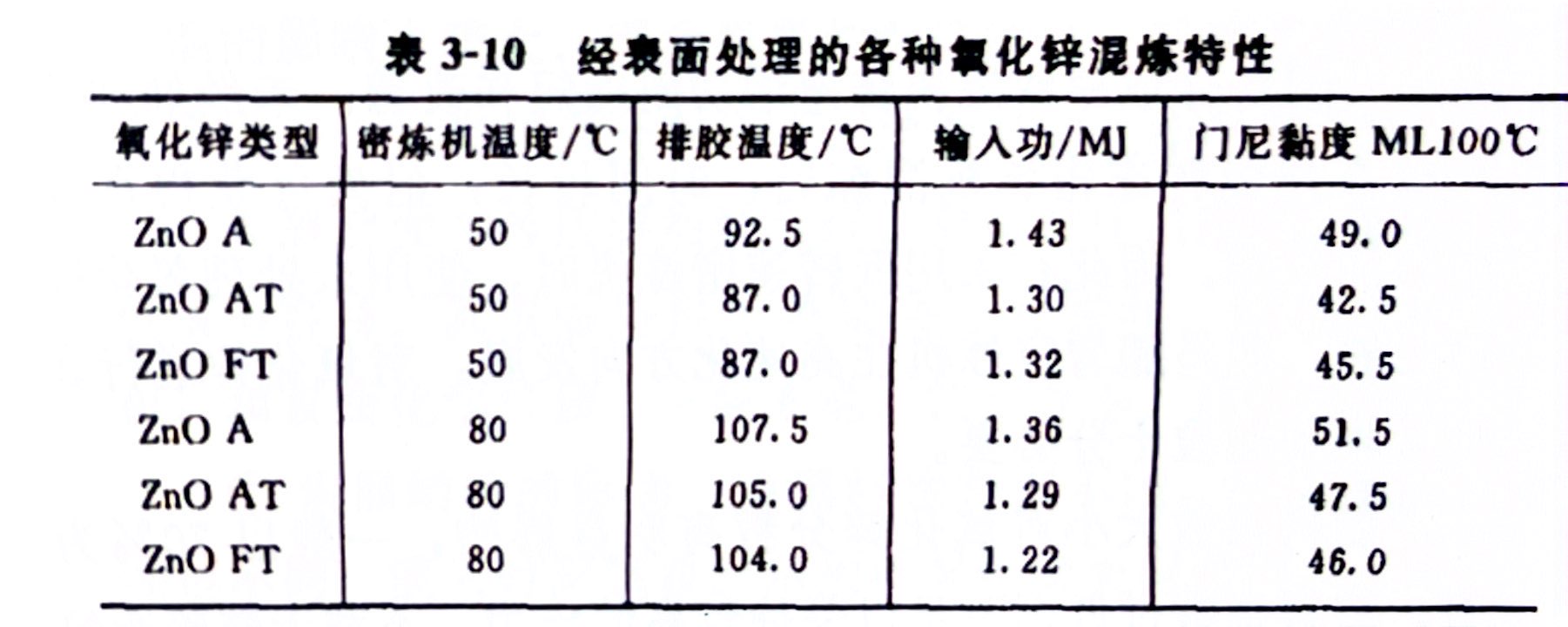
(2)造粒 表面处理和未处理的氧化锌均可造粒。表面处理并造粒的氧化锌混炼性能更好,如氧化锌 ATP(即 ZnO ATP;美国产品)即属此类产品。与未造粒、未处理氧化锌相比,表面处理的氧化锌混炼时间短,所需输人功率低;与未造粒但表面处理的ZnO AT 相比,也显示出类似优点。但是在低转速(20r/min)密炼机中会出现反常现象,即造粒氧化锌的混炼时间反比未造粒者为长,产生这种现象的主要原因是转速低,压力小,从而不利于造粒氧化锌粉碎。此外,未造粒氧化锌在混炼时不能在短时间内聚集到上顶栓下端处,而造粒氧化锌则始终处于上顶栓的底端处,所以能迅速混人橡胶并分散。各种氧化锌在密炼机中的混炼特性见表3-11。
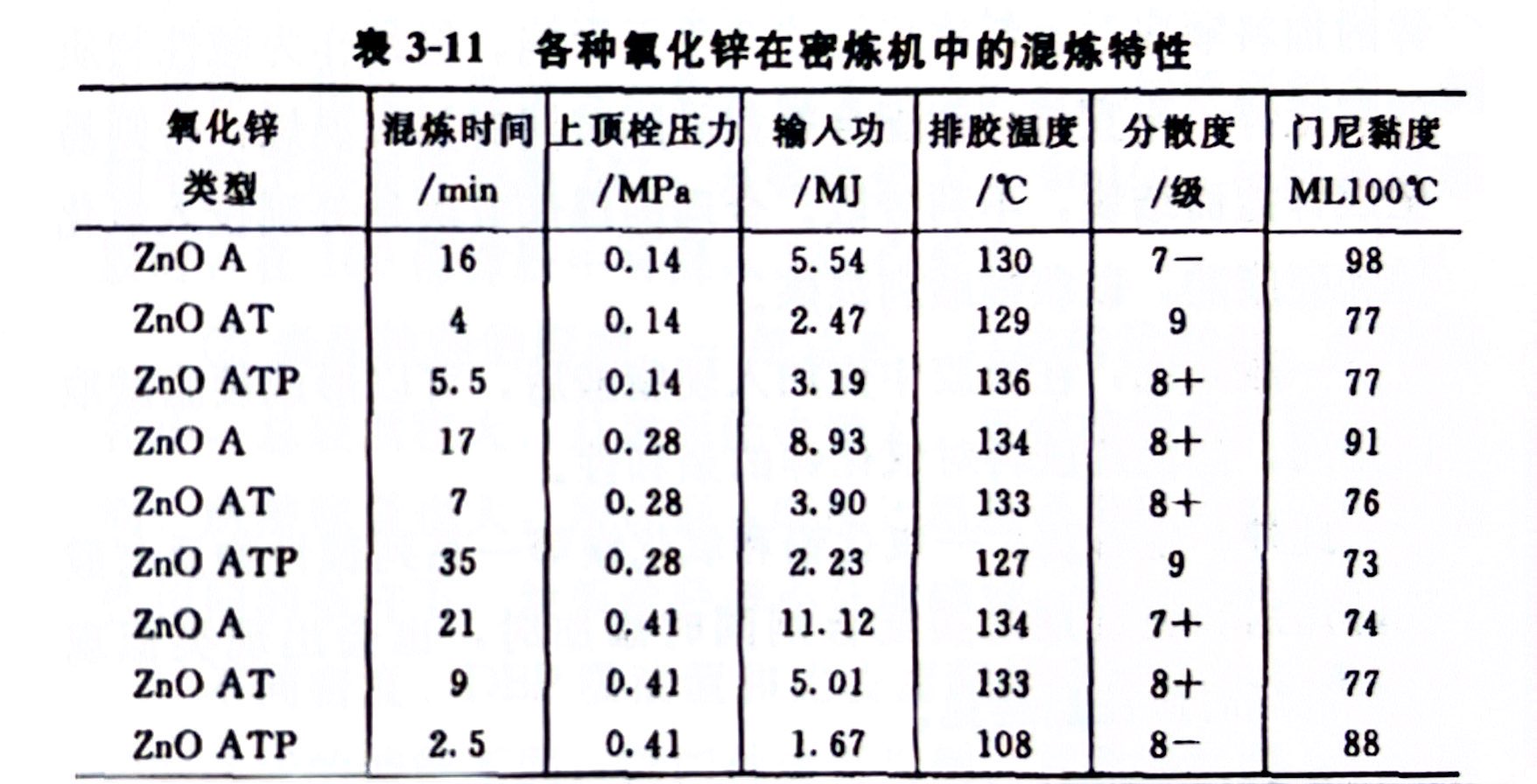
由表3-11可见,经丙酸处理的 ZnO AT 和ZnO ATP 的混炼时间和分散随密炼机转速增加而缩短和改善。未经处理的ZnO A 用慢转速密炼机混炼时,时间较长,但尚可获得良好的分散效果。因此在采用低转速密炼机时,使用未处理氧化锌已足够,但是随着密炼机往高速化方向发展,对氧化锌进行表面处理和造粒十分必要。装料系数大小对氧化锌分散有明显影响,一般以70%为宜。装料系数过低则不足以保持较高的压力,不利于破碎造粒氧化锌并使之混人橡胶。
(3)母炼胶法 对于普通氧化锌,为了提高其混炼分散效果,常采用制造母炼胶的方法,即由氧化锌70质量份和橡胶30质量份组成母炼胶。混炼时氧化锌不要一次加人,宜分几次添加,待先加入的氧化锌混入完毕后再加下一批。在临近混炼结束时,加人少量的水,能提高氧化锌的分散度。采用母炼胶后,很少发现有分散不良的现象。
(4)加料顺序和其他 从分散度来说,在混炼初期加人氧化锌有利于分散,但会缩短焦烧时间。从物理性能来看,氧化锌的加料顺序对胶料物理性能几乎无影响。但是作为碱性物质的氧化锌,不宜与酸性配合剂如硬脂酸同时加人混炼,否则易生成锌盐而结块,不利分散。合理的混炼方法是分别投人氧化锌和硬脂酸,以获得顺利混炼。一般来说,在橡胶中先加入硬脂酸后,可以形成硬脂酸取向排列,能提高胶料对氧化锌的亲和性。此外,生石灰、一氧化铅和氧化镁等一系列碱性物质与酸性防焦剂和促进剂之类配合剂同时添加时,也会出现类似现象,混炼时应注意避免。